Editor
- FMA
- The Fabricator
- FABTECH
- Canadian Metalworking
Identifying the hallmarks of a modern CNC
Make your control the hub of your digital and real-world machining
- By Joe Thompson
- April 19, 2024
- Article
- Metalworking
Computer numeric controls (CNCs) are more than just a computer system, some buttons, and a screen.
Advancement in this technology is transforming the way parts are created. The future of CNCs, which is rapidly approaching, will see a movement toward even more flexible, powerful, and connected systems that will exist at the heart of both digital and practical machining work.
The digitalization of CNC machining combines CNCs, advanced sensors, the Industrial Internet of Things (IIoT), and data-driven processes to transform traditional machine shops into connected, automated production facilities.
This matters because modern CNCs are synchronized to use real-time communication between hardware and software. When this real-time communication is coupled with a machine’s sensors, adaptive machining is possible, and the machine makes adjustments based on real-time data.
Modern CNCs have connectivity that allows them to link to different industrial network systems (fieldbuses), shop floor equipment, and also manufacturing software. This allows for data collection and enables them to connect to third-party devices.
Today’s controllers also offer more programming flexibility and options when compared to their older counterparts. Custom macros, subroutines, and parametric programming enable a level of customization that hasn’t been possible for shops before now.
And the future only brings more technology to the party.
Artificial intelligence (AI) and machine learning (ML) are already being applied, and this will only grow. And cybersecurity, often ignored, will become increasingly important because of the increased connectivity of manufacturing environments.
Computing Power
Most modern CNCs have a data server built into the control with a large memory capacity, often more than 3 GB, and/or additional PC functionality so operators can tap into the large amount of solid-state hard drive space on the PC, which stores and runs programs.
Having a separate PC is an ideal setup because the PC has its own processor; it doesn’t share one with the CNC. This enables fast processing time and gives the user the right amount of memory needed to run complex programs.
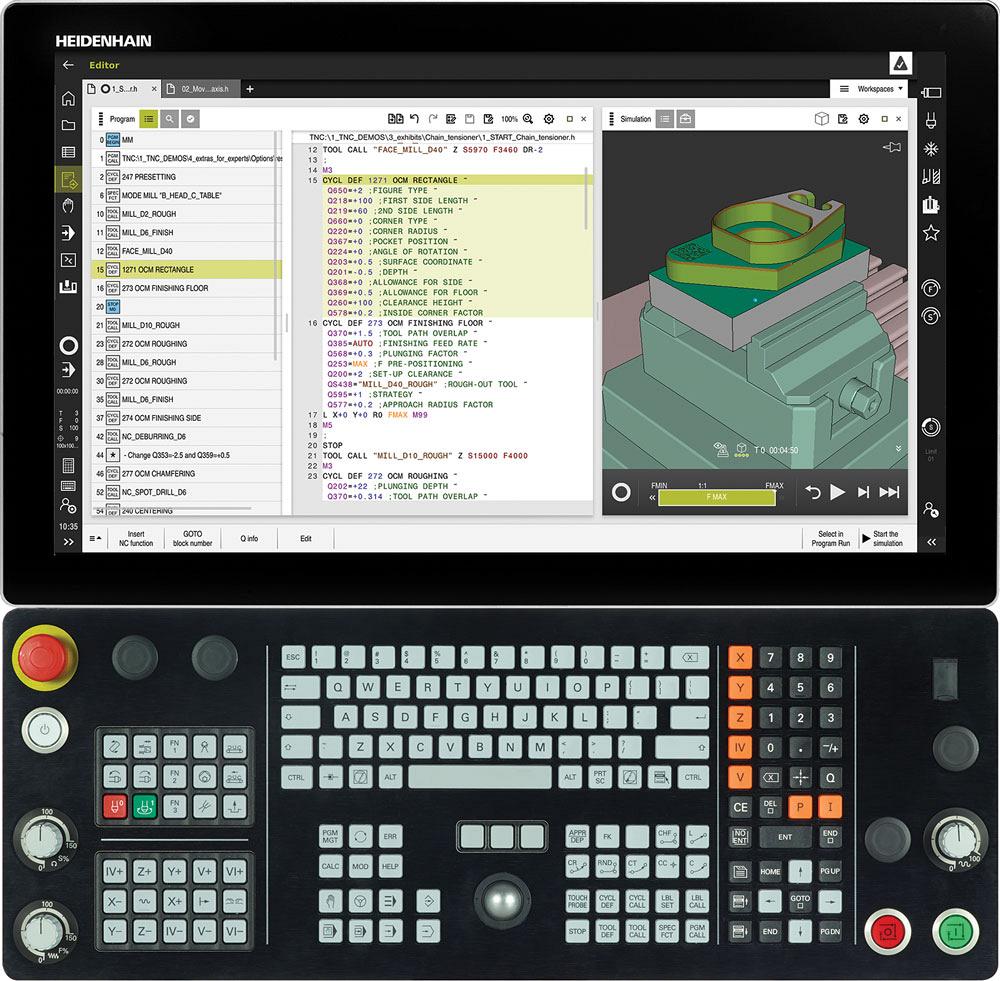
The TNC7 supports users in all scenarios, including programming, machine setup and part measurement. HEIDENHAIN Corp.
But what truly defines a modern CNC? It all starts with connectivity.
Your CNC Is Mission Control
“The control is now becoming a mission control centre. We want to be able to give the operator a system at the machine where they can solve problems on their own without needing to involve the programming department. You want the flexibility to empower the operator to make changes without going through the whole process of waiting for other people,” said Gisbert Ledvon, vice-president of marketing for HEIDENHAIN Corp. “At a minimum, you want to make sure that your control allows you to access your network to load setup sheets and data from your CAM system into the machine without the need for workers to load programs from memory sticks.”
For these reasons, the control needs to be a big part of a company’s digital manufacturing process. It’s more than just a one-way interface. Operators need to be able to do enough work on the control at the machine so that it’s not just a dummy box that imports data so they can then push a button.
“In my opinion, the CNC is the heart of the manufacturing floor,” said John Meyer, marketing communications manager at Siemens. “Every part that is manufactured with traditional machining processes needs to go through the CNC. And without it having a true digital twin, it will inevitably become the bottleneck. Plus, with just-in-time manufacturing, if a company can’t predict and anticipate where issues may arise, they effectively are running blind.”
FANUC also sees digital twin functionality as an important aspect of modern CNCs.
“Setting up a digital twin does take some time because the machine builder has to be involved as well,” said John Horn, national sales director, CNC and motion systems at FANUC America. “But when it’s done right, it’s a powerful tool.”
Using the power of a digital twin, then, is the hallmark of a modern CNC.
“Systems that use AI servo-learning functions are also part of what I would consider a modern CNC,” said Horn. “For example, when a part is running on a machine and you run that part over and over again employing AI servo-learning functions, the control will figure out how to make that part better and faster.”
The AI of the system increases and decreases speeds and feeds, where necessary, to optimize the part to get the best cycle time and also the best precision.
At FANUC, the Plus controls handle complex work. These CNCs include 30i-B Plus, 31i-B Plus, 32i-B Plus, and 0i-F Plus. These controls enable ML on real machines while in process.
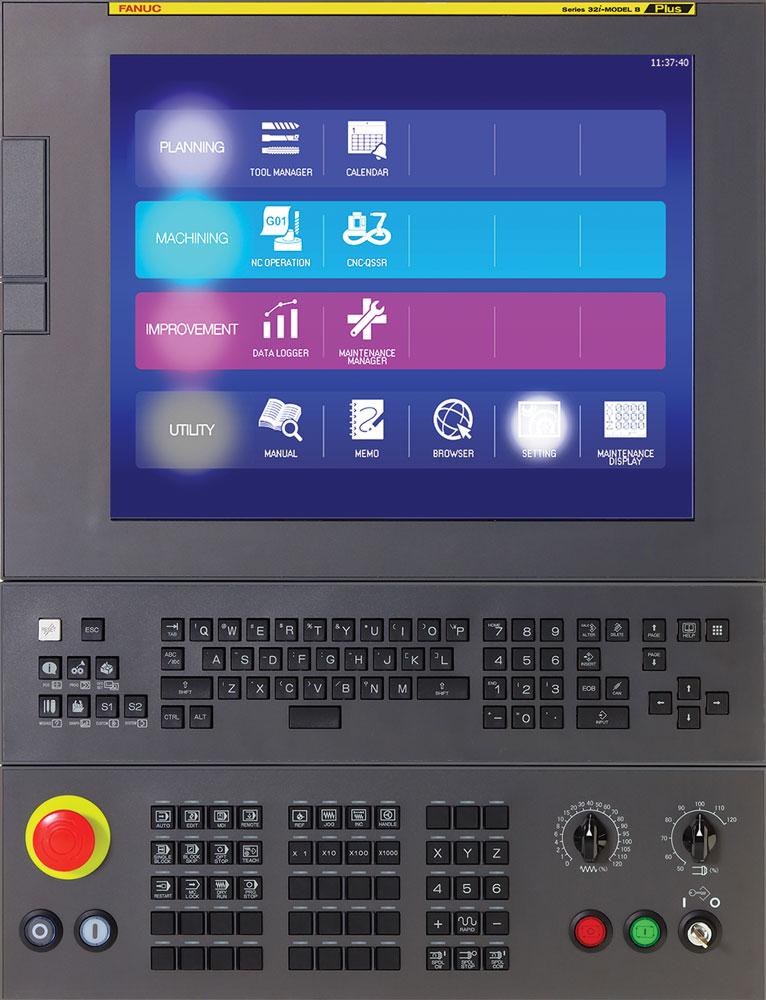
FANUC 32i-B Plus CNCs are designed to maximize and simplify the operations of advanced machine tools. FANUC America Corp.
“At IMTS two years ago, we demonstrated the Plus control with an AI servo-learning function for chip breaking,” explained Horn. “We were turning on a lathe, and instead of making the big, long, stringy chips that wrap around everything, the control’s learning functions monitored the servo load and chopped those chips into little, tiny chips as it was running.”
This type of functionality can only be done by monitoring the load of each axis while it's doing a specific cycle. And, if the CNC can do this work itself, it eliminates the need to send the machine data out to a PC and run it on a piece of software before sending it back to the machine.
“It's just much better if the machine can learn from what it's doing,” said Horn.
AI and ML, it seems, has a role to play in the future of CNCs as well.
Complex Machines Require Complex Controls
Turn/mill, mill/turn, full 5-axis machining (and beyond), and hybrid additive/subtractive machine tools are all complex systems that make complex motions. Hybrid machines perform traditional subtractive machining operations on a part that was just created additively.
“The CNC needs to be able to adapt to these emerging technologies to truly be considered modern,” said Meyer.
Siemens’ latest entrant into this space is the SINUMERIK ONE. It is the first control completely developed in a virtual environment—even before it was manufactured in the real world.
“Machine users benefit from this environment where they know exactly what the machine is going to do before they ever get in front of the real one,” explained Meyer.
As machine tools advance, new high-performance toolpaths become available to programmers, and the controls have to keep pace.
“It is becoming even more critical that CNCs have a super-high block process time. This will ensure that the system does not pause due to a lack of data,” said Meyer.
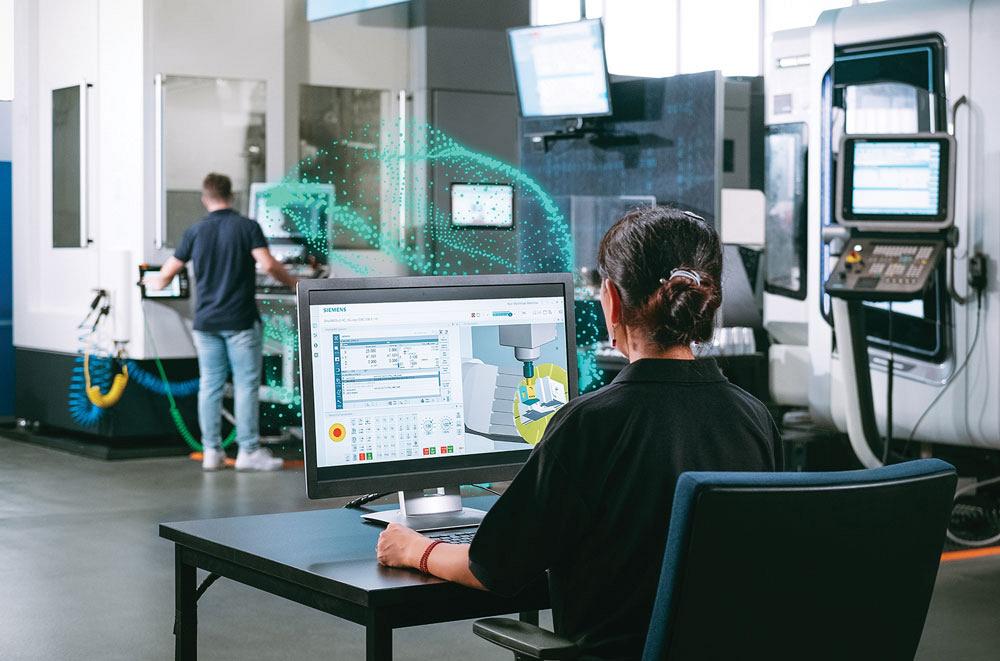
Siemens will accelerate digitalization for a sustainable tomorrow by demonstrating how the potential for optimized machine tools can be seen, thanks to the improvements in its digital native CNC platform. Siemens
According to Meyer, the SINUMERIK control runs splines natively, not in a point-to-point method.
“This means that, even if they convert geometry into splines, they still need to linearize the code before the part program is run. The SINUMERIK CNC does not do that. Internally, all motion is resolved to be a spline. This allows the machine user to run very sophisticated geometry with the least amount of data needed,” Meyer added.
Be Conversational
Conversational programming is something that most control systems have been able to do for some time, but many still consider it a modern convenience.
Being able to program right at the machine without having to type in a large amount of G-code saves a lot of time. Using menu-based conversational programming for fairly simple parts can even eliminate the need for the part to go through the programming department.
“By taking advantage of embedded cycles and functions, you keep the program shorter, and the control calculates cycles much faster because it looks at that cycle and doesn’t have to read so many lines,” said Ledvon.
It simplifies the creation of simple parts and is intuitive and can be graphically based.
“You can actually walk up to a HEIDENHAIN control now and make, for example, a small bracket. You can draw it with your finger right on the screen, and the control writes the program for you,” said Ledvon.
Be Customizable
With great computing power comes great flexibility. And HEIDENHAIN is taking advantage of both computing power as well as screen technology.
“With the TNC7, we walked away from the traditional CNC design concept. We now give the operator the freedom to design and configure the control the way they like it,” said Ledvon. “We designed it more for the end user rather than the machine tool builder.”
FANUC also supplies CNCs with customizable interfaces so that the machine tool builder can modify the look and feel of the machine control that they want to provide to their customers.
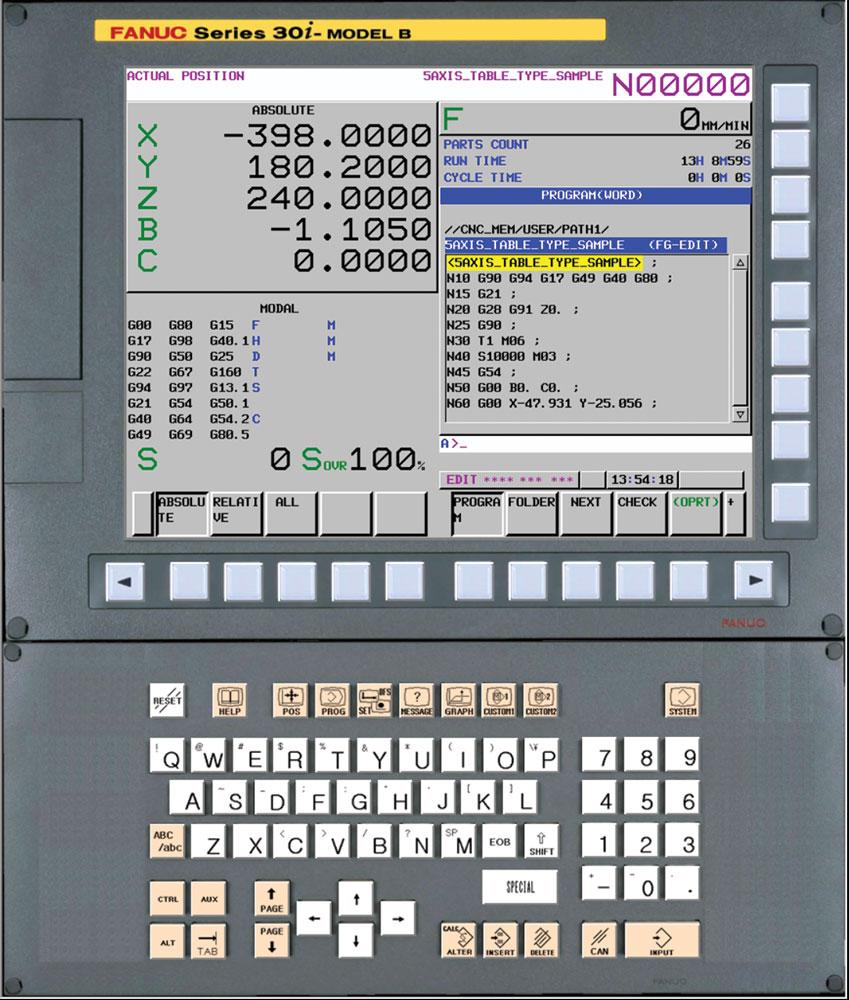
CNC Guide simulates the FANUC CNC for part program creation, G-code testing and optimization all via a PC. FANUC America Corp.
“The machine builder can tailor the control in any way they want by writing their own front-end interfaces,” said Horn. “It doesn't have to look like a standard stock FANUC CNC front-end interface.”
Use Guides and Videos
CNC manufacturers want their users to get the most out of their controls. The latest technology includes help guides and training videos.
“We have a software called CNC Guide, which allows our customers to set up their ‘CNC’ on a laptop,” said Horn. “They enter their programs and parameters and can now test different options without tying up the real CNC at their machine. They may have a tricky 5-axis feature, and with the digital twin through CNC Guide on their laptop, they're able to test out different kinds of functions.”
The HEIDENHAIN control also has a feature that can teach the operator right at the machine.
“We included video tutorials within the control that can show you how to pick up a part or how to calibrate a 5-axis machine,” said Ledvon. “It becomes very intuitive when you watch the video and then apply it to your actual process. The videos guide operators through the steps they need to take and can actually help them write a program.”
Digital Transformation
Too many buzzwords create information overload, and in the manufacturing sector, digital transformation is often being delayed because shop managers think they don’t need all the fuss. But digital transformation is happening whether they know it or not.
The best advice? Start small.
“We tell manufacturers: Just start,” said Horn. “Even if that means just recording your stack light information. Start tracking every shift whether the spindle is running or not, if it’s ready or in a warning state. And start tracking what machines are doing better than others so you can start to understand why.”
This type of information is easy to get with machine tool monitoring and data collection systems like FANUC’s MT-LINKi, HEIDENHAIN’s StateMonitor, and Siemens’ Machine Monitor.
Cybersecurity Matters
It’s making headlines every day in every industry, so it’s not surprising that cybersecurity is becoming more important to connected devices in the manufacturing sector.
“FANUC CNCs have an option called eight levels of protection. It allows eight different passwords to be used in the CNC system,” said Horn.
These get set by the machine tool builder originally.
“The first level can allow the operator to load programs, the second-level password allows them to edit programs, the third level lets them change parameters, and so on,” said Horn.
Horn hinted at future security features that will soon be a part of FANUC’s systems: passwords, QR codes, and even facial recognition.
Digital Machining Environment
Safety doesn’t just include outside influences. What happens inside the machine matters most. And that means not breaking stuff.
Most collision monitoring setups show how the machining envelop currently exists. When a program is run, it checks to see if there will be a collision.
While collision monitoring and collision avoidance has been part of programming and part processing for some time, the use of digital assets ups the ante by once again making use of real-time data and in-machine probing.
“Let’s say you have a job set up on a machine, but then you need to do another job,” said Ledvon. “We can now load a 3D model of a vice and using the touch probe, determine where this vice actually sits in that machine envelope.”
Once the probing cycle is finished, that 3D model in the machine gives the control enough information to know if there will be a collision or not.
“During this process, you need to make sure that the data you're getting from your measuring devices is coming as fast as possible to your control, because your control is working very fast processing that data to move the tool,” said Ledvon. “The tool has to be in a certain spot at a certain time within a fraction of a second. Any type of delay in data flow into your control will slow down the process.”
A digital transformation journey shouldn’t be a pain point for a manufacturing business. Modern CNCs, and the functions they perform, are organically pushing shops forward in this area. Digital twin creation, machine monitoring, and connecting shop assets is a part of the digital transformation process. And the good thing is CNCs are already doing this for you.
Editor Joe Thompson can be reached at jthompson@fmamfg.org.
FANUC America Corp., www.fanucamerica.com
HEIDENHAIN, www.heidenhain.us
Siemens, www.siemens.com
About the Author
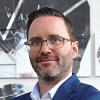
Joe Thompson
416-1154 Warden Avenue
Toronto, M1R 0A1 Canada
905-315-8226
Joe Thompson has been covering the Canadian manufacturing sector for more than two decades. He is responsible for the day-to-day editorial direction of the magazine, providing a uniquely Canadian look at the world of metal manufacturing.
An award-winning writer and graduate of the Sheridan College journalism program, he has published articles worldwide in a variety of industries, including manufacturing, pharmaceutical, medical, infrastructure, and entertainment.
Related Companies
subscribe now
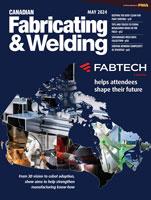
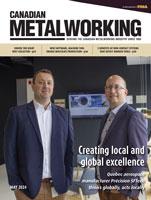
Keep up to date with the latest news, events, and technology for all things metal from our pair of monthly magazines written specifically for Canadian manufacturers!
Start Your Free Subscription- Trending Articles
Sustainability Analyzer Tool helps users measure and reduce carbon footprint
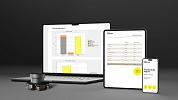
GF Machining Solutions names managing director and head of market region North and Central Americas
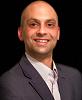
Mitutoyo updates its end-user portal
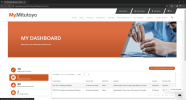
Enhance surface finish with high-speed machining
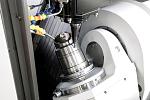
Portable 3D scanners offer adjustable scanning distance, advanced volumetric accuracy
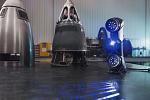
- Industry Events
Automate 2024
- May 6 - 9, 2024
- Chicago, IL
ANCA Open House
- May 7 - 8, 2024
- Wixom, MI
17th annual Joint Open House
- May 8 - 9, 2024
- Oakville and Mississauga, ON Canada
MME Saskatoon
- May 28, 2024
- Saskatoon, SK Canada
CME's Health & Safety Symposium for Manufacturers
- May 29, 2024
- Mississauga, ON Canada