Associate Editor
- FMA
- The Fabricator
- FABTECH
- Canadian Metalworking
Shop shows a talent for coating
ACL prides itself on being a driver of innovation in the coating industry
- By Lindsay Luminoso
- May 13, 2021
- Article
- Fabricating
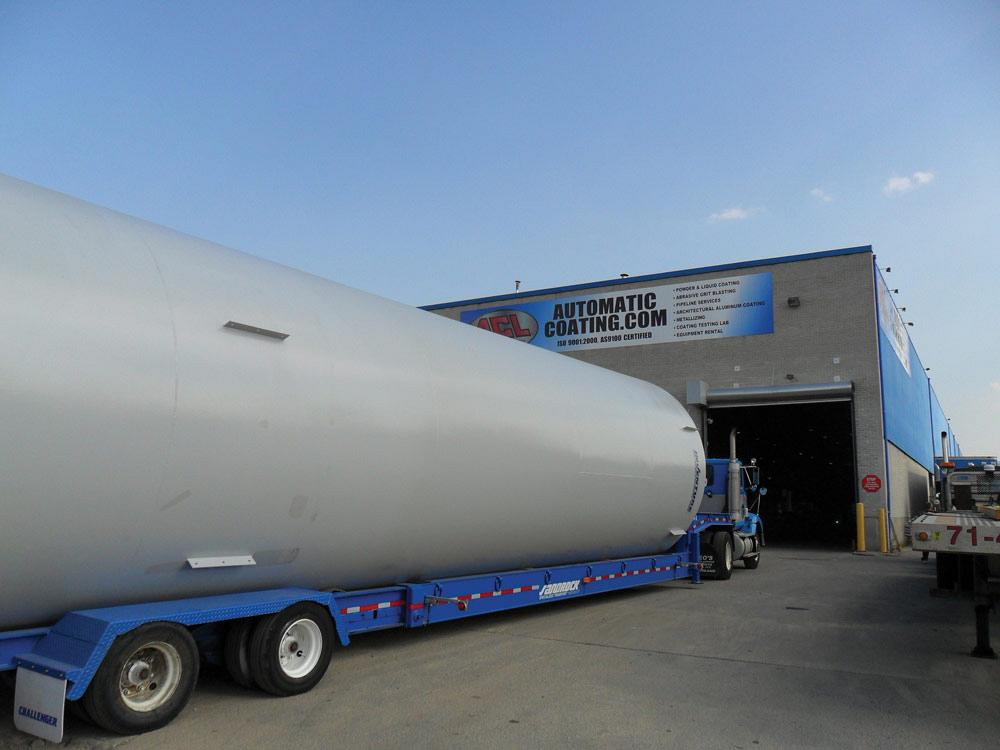
ACL can handle and coat very large components that other coating shops might not be able to. It also takes on small jobs, field work, and everything in between. Images: Automatic Coating Limited
When most people think of manufacturing in Ontario, they often immediately think of Toronto and surrounding areas. That is not to say that manufacturing doesn’t occur outside of the GTA, in places like Windsor, London, and Hamilton, but according to Statistics Canada, the Toronto Census Metropolitan Area (CMA) accounts for the largest amount of manufacturing sales in the province and beats out every other CMA in the country.
The GTA has significant sectors that help keep the manufacturing industry thriving. Many of its industrial facilities are clustered in the Mississauga area and spread out across the west end of Toronto. But Jocelyn Bamford, vice-president of Automatic Coating Limited (ACL), wants everyone to know that Scarborough is not to be overlooked.
"We have such a great thing going on in Scarborough," she said. "It is a hub of great manufacturers with great dedication and great technology. We are all each other’s customers and each other’s suppliers, and with very little effort, we could really start to see Scarborough being a thriving manufacturing and industrial hub."
ACL
Located in a 75,000-sq.-ft. facility in Scarborough, ACL specializes in coatings, offering liquid and electrostatic powder coating, along with a patented tidal coating fluidized bed. The company also has a field coating group located in Edmonton where workers are focused on integrity work for pipelines.
"In North America pipelines are ubiquitous," said Bamford. "They are everywhere but tend to have some lifespan issues. Our team can go in, the contractor digs up the pipe, and an inspector comes in to inspect. If there are any stress cracks or corrosion, the part or piece can be replaced, and we recoat it before it is put back in the ground."
Across all of its divisions, ACL employs just under 100 people. Workers have a range of skills, from engineering, quality assurance, and fabrication to sales and accounting. However, the company is focused on R&D—developing new patents and new technical expertise—and this continues to be one of its fastest-growing areas. But a coating company wouldn’t be successful without highly skilled paint sprayers, which Bamford says is a very niche and highly technical area.
"Spraying, as you can imagine, is really an art form," said Bamford. "We get very large components that need to be coated in liquid, and that requires a lot of skill. You need to make sure that you have consistent quality throughout the piece and that you don’t have sags or drips. You also need to make sure that it’s very precise. That’s more on the liquid side of coating."
Even though most of ACL’s electrostatic coating is automated, Bamford said that the company still needs highly skilled employees with a great eye for detail to catch any areas that are missed or errors during the coating process, as these missed areas need to be touched up manually.
“It's one of the hardest skills and one that's in great demand in a lot of industries,” said Bamford. “And there's no real training for it, which is challenging because it’s a very high-demand skill set. The only place that offers something similar is automotive spray training at Centennial College, which is a completely different skill set. So, for us it's a high-demand, very technical niche area, and we are always looking for good sprayers.”The company is able to distinguish itself as a leader in the coating world because of its full-service lab. ACL not only performs coating services, but also offers a panel service in which a panel is coated and tested to make sure that it is high quality and will hold up in the field. The shop’s lab can perform over 50 different tests to ensure the coating is exactly what the customer needs.
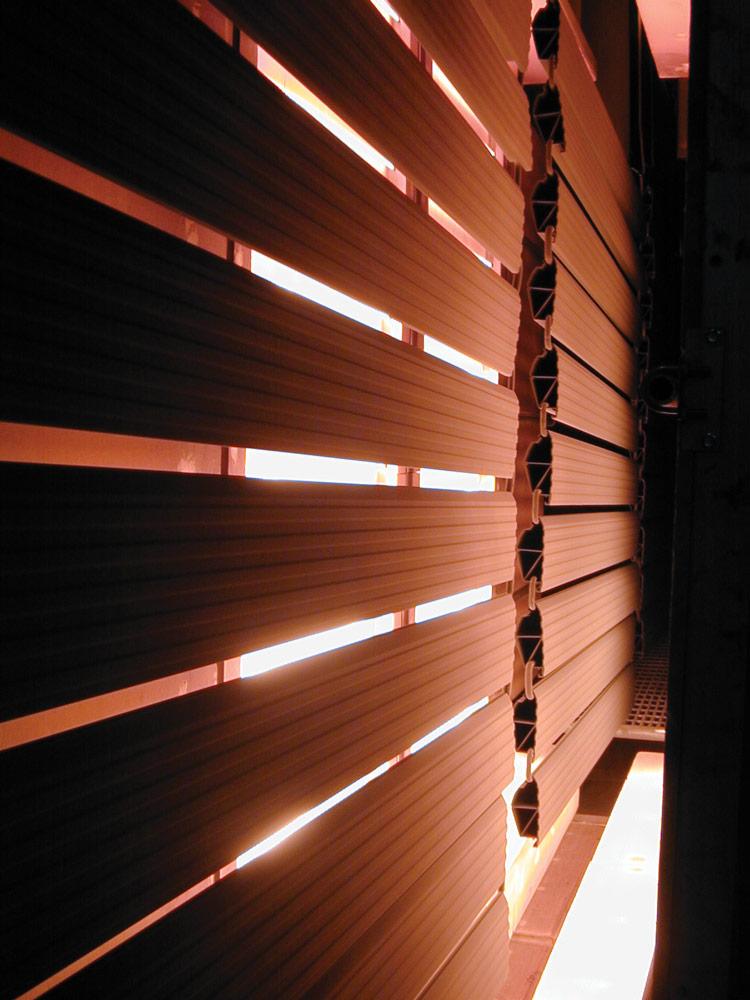
Spraying is really an art form, said Jocelyn Bamford. Both liquid and electrostatic powder coating require a lot of skill.
"From our patented tidal coat to electrostatics to liquid, we can handle just about any job," said Bamford. "And we have huge overhead crane capacity and a large space. We can handle very large pieces that other coating shops might not be able to handle, so we can do big parts and small jobs and everything in between."
Coating Projects
Almost all projects that come through ACL’s door have some sort of engineering specifications built into the design. Still, the shop will work with the customer to discuss the best coating options for a given project. Not all engineering specs make sense in real-world applications, and Bamford noted that they are able to work with the customer to see if a certain paint technique or specification can be adjusted for better results.
"We really take a step back," she said. "We start by looking at the part, at its requirements for life cycle and longevity, where it’s going to be placed, whether indoors or outside, if it will be exposed to salt water, and so many other variables. We take a consultative approach and make recommendations based on our years of experience to ensure that the customer is getting exactly what they hope to achieve."
For the most part, pipelines have a liquid-type coating specification as do pipe spools and fittings that go into the resource sector. ACL also offers some proprietary coating options, including one for the mining industry that the company boasts can triple the life cycle of a part.
The company’s patented tidal coating is designed for anybody with a ship in the water who doesn’t want to see their part corrode.
Tidal Coating
"The majority of people who come to us have a coating in mind," said Bamford. "However, there are some cases, like that of the U.S. Navy, who came to us when they had an issue that needed to be solved. We used to do work for a large contractor that produced transducer tubes that provide the pinging noise when a ship is out at sea. We coated the housing and a U.S. company coated the actual transducer tubes. What ended up happening was salt water got into the transducer tubes and shorted them out. But our housings were perfect."
The U.S. Navy asked ACL to devise a coating for the transducer tubes, which ACL was able to develop, and apply over the last 20 years. From this technology ACL developed a tidal coat system for air intake and uptake louvre and watertight doors, which it then patented.
This tidal coating can be applied to any part that has the potential for extreme corrosion, especially those being exposed to salt water. The company went further and developed a piece of equipment for the Navy to use in their own coating shops that will coat a watertight door automatically in two minutes.
"It’s state-of-the-art and all PLC," said Bamford. "It will give first-pass quality and a 10-year life cycle for a watertight door."
R&D
ACL has always prided itself on being a driver of innovation in the coating industry. It has spent years dedicated to developing world-class patents to extend the life cycle of parts. It recognized early on that having a mobile field unit to coat on-location in pipeline country would help make the industry safer and more efficient.
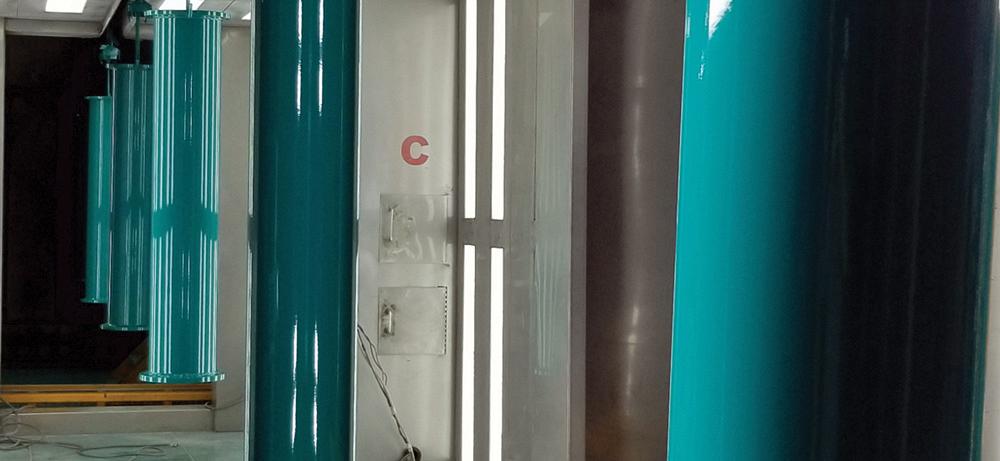
In addition to liquid-type coatings for pipelines, ACL also offers proprietary coating options, including one for the mining industry that the company boasts can triple the life cycle of a part.
The company has also focused on making itself more environmentally friendly. It developed a coating rig that initially had three diesel engines and pared it down to one engine, reducing the greenhouse gas emissions by upwards of 50 per cent.
"We also developed a way to take off old coatings that may contain PCB, asbestos, or coal tar," said Bamford. "We encapsulate the old coating so that it does not leech into the environment. We are currently working on developing a girth weld coater for pipes that require coating, and it’s important to us that this coater is solvent-free. It’s all about longevity and being environmentally friendly. It’s a really exciting time and there is just so much innovation ahead of us."
Innovation Hub
While ACL has focused much of its attention over the years on R&D related to coating, it has spent the last year working with local fabricators and manufacturers to create an industrial hub focused on developing innovation. The company has been working closely with Samco Machinery, which recently opened a new fabricating division in Toronto, Ont.
"Many of the projects we have coming in have been fabricated locally and we coat them," said Bamford. "There’s a lot of back and forth between us and local manufacturers, which has led us to look for other areas of opportunity where we can work together for innovative new projects and world-class services. We are really looking to develop Scarborough as a hub for innovative technology."
Bamford noted that she sees the current market trends as an opportunity for the local community and Canada to really make itself an industrial hub and bring manufacturing back and elevate it to the status it deserves.
"What we really need is a strategy to maintain and grow manufacturing because manufacturers really build things that bring money into an economy," she said. "That’s what we are trying to do in Scarborough with partners like Samco, and that’s what we should focus on as a country."
A Local Focus
Samco Machinery, a manufacturer of roll forming machines located in Toronto, has focused its attention on developing new ways to support its customers. And one way it did this was investing in a fabrication division to build on its vertical integration and support its need for part production capabilities.
This fabrication segment allows the company to fabricate parts in-house for machines and build assemblies as required. The facility can fabricate all part sizes, weld, and build assemblies, and it includes crane capacity to lift up to 100,000 lbs., oversized shipping doors, and 33-ft. ceilings.
With this new division, Samco has recognized the need to support and grow the local manufacturing sector. With many of its customers and partners located in Toronto, the company has spent many months developing relationships with companies like ACL to showcase the city’s manufacturing capabilities.
"Samco and ACL are working together to make the region a hub for innovation," said Noli Cusi, vice-president of the Fabrication Division, Samco Machinery. "We are continually advancing technologies within the organization. Samco’s mandate is to continually innovate and improve processes and engineering, mechanical and electrical technology within the machines we produce and the parts we manufacture. ACL is a leader in the powder coating industry. Both companies work with a variety of industries such as building and construction, military, mining, and automotive. Together with our combined expertise in metal forming and coating, ACL and Samco can build on the existing relationship and grow to provide a hub for innovation in the Scarborough area that can service global distribution as needed."
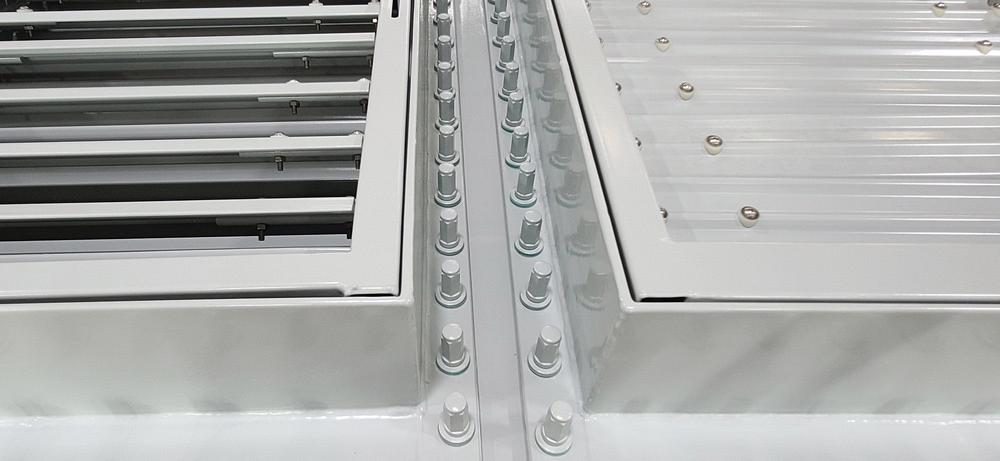
The company’s patented tidal coating can be applied to any part that has the potential for extreme corrosion, especially those being exposed to salt water.
Proximity of expertise is important to build on understanding the manufacturing process. Companies in the city are working together and collaborating to improve and adapt manufacturing practices and develop coatings as customers require.
"We are really excited about this partnership, but we are most excited to help customers find the right fit for their manufacturing needs," said Cusi. "Our goal is to identify an opportunity and assign a team to ensure the process is efficient, meets and exceeds requirements, and adds value. In addition, job creation and expertise will grow to help sustain and develop the industry and keep the Canadian market strong."
Associate Editor Lindsay Luminoso can be reached at lluminoso@canadianfabweld.com.
Automatic Coating Limited, www.automaticcoating.com
Samco Machinery, www.samco-machinery.com
About the Author
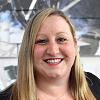
Lindsay Luminoso
1154 Warden Avenue
Toronto, M1R 0A1 Canada
Lindsay Luminoso, associate editor, contributes to both Canadian Metalworking and Canadian Fabricating & Welding. She worked as an associate editor/web editor, at Canadian Metalworking from 2014-2016 and was most recently an associate editor at Design Engineering.
Luminoso has a bachelor of arts from Carleton University, a bachelor of education from Ottawa University, and a graduate certificate in book, magazine, and digital publishing from Centennial College.
Related Companies
subscribe now
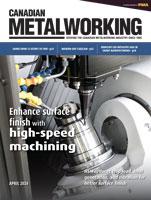
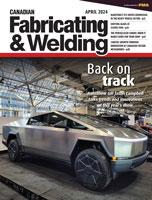
Keep up to date with the latest news, events, and technology for all things metal from our pair of monthly magazines written specifically for Canadian manufacturers!
Start Your Free Subscription- Trending Articles
Aluminum MIG welding wire upgraded with a proprietary and patented surface treatment technology
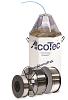
Achieving success with mechanized plasma cutting
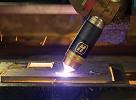
Hypertherm Associates partners with Rapyuta Robotics
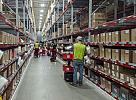
Gema welcomes controller

Brushless copper tubing cutter adjusts to ODs up to 2-1/8 in.
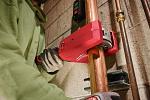
- Industry Events
MME Winnipeg
- April 30, 2024
- Winnipeg, ON Canada
CTMA Economic Uncertainty: Helping You Navigate Windsor Seminar
- April 30, 2024
- Windsor, ON Canada
CTMA Economic Uncertainty: Helping You Navigate Kitchener Seminar
- May 2, 2024
- Kitchener, ON Canada
Automate 2024
- May 6 - 9, 2024
- Chicago, IL
ANCA Open House
- May 7 - 8, 2024
- Wixom, MI