Freelance Writer
- FMA
- The Fabricator
- FABTECH
- Canadian Metalworking
Speeding up panel production at Signé Hurtubise
Drummondville-based company cuts delivery problems by bringing panel fabrication in-house
- By Mark Cardwell
- September 14, 2022
- Article
- Automation and Software
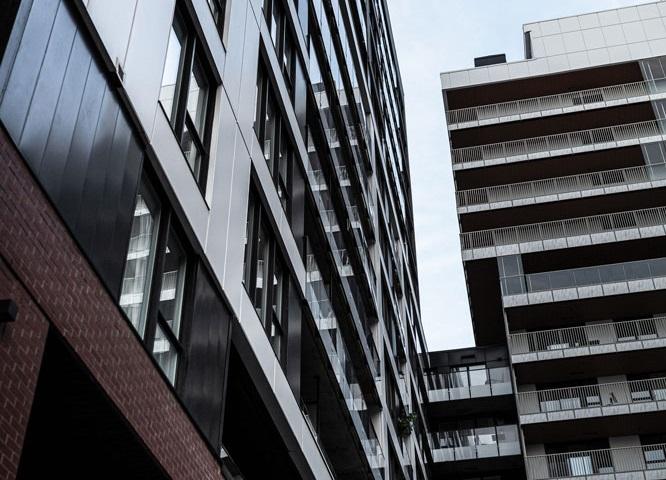
Signé Hurtubise has a 70,000-sq.-ft. facility dedicated entirely to the production of aluminum panels used in facades like those seen in this photo. Images: Signé Hurtubise
Quebec entrepreneur Pierre-Olivier Beaulieu doesn’t fool around when it comes to overcoming challenges his burgeoning building envelope companies face.
A good example of this is how he dealt with the holdups he was experiencing several years ago for the manufacture and delivery of aluminum panels to his two Drummondville-based companies—Beaulieu Revêtement and Signé Hurtubise. The panels were needed for the commercial building contracts they were landing in and around Montreal.
“We relied on local metal fabricators, but we were experiencing long delays and communications were always difficult,” said Beaulieu, a 33-year-old husband and father, with a team of nearly 250 employees. “It was a problem we needed to solve, and it got us thinking about how to do that.”
That process eventually led to the 2021 construction of a new $22-million manufacturing plant and offices for Signé Hurtubise in an industrial park in Drummondville, a five-minute drive from Revêtement Beaulieu’s facility.
Entrepreneurial Drive
The heart of the 70,000-sq.-ft. facility, which became operational in October and is dedicated entirely to the production of aluminum panels, is a Salvagnini S4+P4 flexible manufacturing system (FMS).
The touch-free automated FMS punches, shears, and panel bends metal—in this case aluminum—to make panels for Beaulieu’s businesses as well as for other companies, including its competitors.
“It gives us a real advantage in the marketplace,” Beaulieu said about the new plant, which also is equipped with a robotic welding system and an environmentally-friendly powder coating system.
“Delays for aluminum panels from suppliers are usually eight to 16 weeks,” said Beaulieu. “Us? We deliver within two weeks.”
In addition to a leg up on the competition, the manufacturing capacity of Beaulieu’s new FMS-centred facility is helping to bring his dream of becoming a leader in all stages of exterior siding design one step closer to reality.
That vision was a blurry one back in 2012 when Beaulieu, then a 21-year-old student in the two-year building evaluation program at the cégep (college) in Drummondville, did a work placement at a local exterior siding company called Revêtement Louyse.
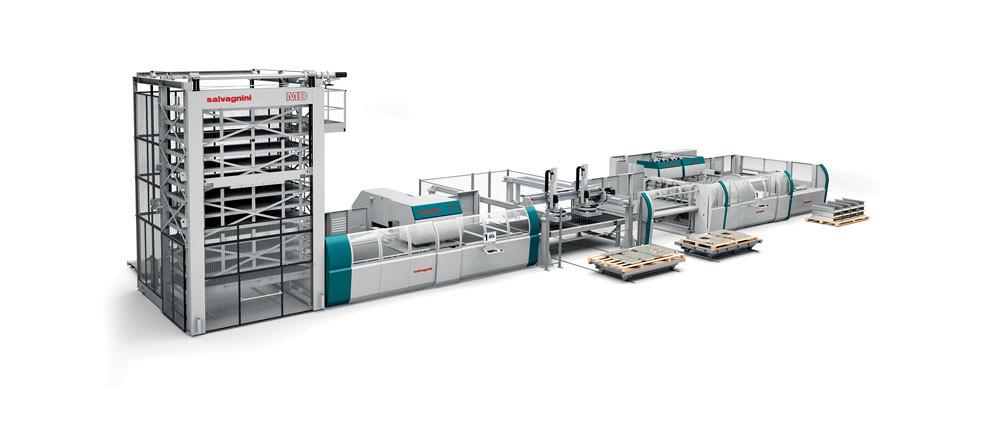
Most start up fab shops build gradually with a punch or laser and a press brake or standalone panel bender and grow their business as money and customer base allows. But as an already busy business concern, Beaulieu knew that such a piecemeal approach would be counterproductive to the gains he wanted to achieve. Instead, he invested in a Salvagnini S4+P4 flexible manufacturing system (FMS). Salvagnini
From the get-go, Beaulieu, a budding entrepreneur, said he loved working in the family-owned business, which was named after the founder’s wife and did mostly vinyl siding in the residential sector in and around Drummondville, an hour’s drive east of Montreal.
But also, he saw the potential for the company to expand and grow its offerings and services in the exterior siding industry, particularly in the commercial sector.
“I always wanted to be my own boss and to do projects in real estate and construction,” said Beaulieu. “I had to start somewhere, and I figured I could grow the company by finding and doing bigger jobs, especially in the Montreal area.”
With bank backing, Beaulieu bought the ten-employee company in 2013 and promptly renamed it Beaulieu Revêtement. He also bought more trucks and equipment and began bidding and landing contracts for commercial exterior siding installation, notably for aluminum and granite.
Aluminum Focus
Eager to expand and desirous for bigger jobs, Beaulieu soon decided to both focus on and specialize in the sale and installation of aluminum panels. “It seemed like every client was asking for aluminum,” recalled Beaulieu. “So if we wanted to grow, we needed to go into aluminum.”
Around the same time, Beaulieu founded a second company – named Signé Hurtubise in honour of his wife’s family – that began to regroup drafting technicians and other building and construction industry experts who could offer a range of turnkey products and centralized services under one roof for commercial building envelope systems – everything from designs and product sales and demonstrations to delivery, installation, and training – for general contractors, architects, and real estate developers.
“From its very beginnings,” reads the company’s website, “Hurtubise was meant to be synonymous with unwavering know-how, passion, and creativity to produce high-quality, custom products.”
For its part, Beaulieu Revêtement, which is the installation arm of Beaulieu’s burgeoning business empire, is described on its website as “the service provider for complete residential and commercial building envelope solutions in Montreal and the surrounding area.”
The weak link in the chain, however, turned out to be Beaulieu’s companies’ reliance on a network of small- and medium-sized local metal shops for the timely production and delivery of aluminum panels for installation (by Beaulieu Revêtement) on everything from schools, stores, and community centres to industrial plants and condominium towers.
Already in 2014, Beaulieu, who had no previous experience in manufacturing, had considered building a state-of the-art plant to build his own aluminum panels. “The concept was to solve a big problem for our clients and many other people in the construction industry, which is delays in delivery,” said Beaulieu. “You resolve that, and you help a lot of people.”
Starting With Automation
With the blessing of his five silent partners and input from both manufacturing and production workflow experts, Beaulieu spent the next few years doing research and laying the groundwork to build a manufacturing plant for aluminum panels.
Most start up fab shops build gradually with a punch or laser and a press brake or standalone panel bender and grow their business as money and customer base allowed. But as an already busy business operation, Beaulieu knew that such a piecemeal operation would be counterproductive to the gains he wanted to achieve.
“We knew what we wanted to do,” said Beaulieu. “And we needed machines and systems that could do the work fast and do both standardized and custom jobs.”
In late 2019, he and a small group of employees and advisors went to FABTECH at Chicago’s McCormick Place. It was at that show that Beaulieu signed a deal to buy Salvagnini’s S4+P4 line.
First developed in the 1970s, the Italian-made FMS remains a popular and efficient machine tool for automatic punching, shearing, and bending of sheet metal.
The FMS was installed last year in Beaulieu’s new plant, which received $5.2 million in loans from the Quebec government to build and equip.
“The competitiveness of SMEs is a determining issue for the health of Quebec’s economy,” said Pierre Fitzgibbon, the province’s minister of economy and innovation, when the loans were announced in Oct. 2020. “Private investment in innovation and new technologies is the key to success for Quebec businesses. I hope today’s announcement will convince other entrepreneurs to invest in their productivity and future.”
Fully operational in October, the FMS uses Salvagnini’s FACE system, which organizes controls the same way for both the S4 and P4 machines. Once programmed, the system first chooses and locates a set of aluminum sheets in the MD store (a storage tower that feeds the S4 punch and shear machine) and delivers them to the S4.
The S4 system uses a multipress head with nearly 100 independent, self-loading punches that are always ready to work, including simultaneous punching of metal parts.
Once the S4 has finished, parts move by conveyor to the P4 for panel bending. Once that’s done, they move to an unloading area.
Depending on the order, panels go for welding by a robotic arm and are then painted using long-lasting, environmentally friendly electrostatic powder painting instead of traditional aluminum siding paints.
Beaulieu said it takes “about 30 seconds to a minute” for his FMS to make an aluminum panel—depending on the number of punches and bends needed—once an order is loaded by Signé Hurtubise’s team of programmers and the start button is pushed.
Once complete, orders are delivered by one of two 24-ft. trucks dedicated to the delivery of aluminum panels across Quebec. Out-of-province orders are shipped by third-party carriers.
Business Expansion
In addition to orders generated by the company’s in-house sales team for turnkey building envelope packages, orders also can be placed by customers who go through the company’s recently launched online portal—a new feature Beaulieu believes will help spur demand and growth in other jurisdictions.
This year the company notably launched its products and services across Canada and already has signed a client in Ontario’s GTA. Next year, it plans to penetrate the U.S. market also.
For Beaulieu, the ability to make his own aluminum panels using a fully automated FMS was a winning move that is paying big dividends—bigger than even he imagined.
“Because the system is automated, we need less staff, which is a huge advantage in the current labour market,” said Beaulieu. “We also have our own training centre where we can teach people in both the classroom and in the plant for periods of two weeks to seven months, depending on the job they do.
“Things have worked out great for us so far and the FMS gives us some huge advantages over the competition and has given us many new opportunities to explore and develop,” said Beaulieu. “We’re working hard to continue growing our company, and our new manufacturing ability is a big step forward.”
Contributing writer Mark Cardwell can be reached at m.cardwell@videotron.ca.
Beaulieu Revêtement, beaulieurevetement.com
Signé Hurtubise, signehurtubise.com
Salvagnini America, www.salvagnini-america.com
Visit canadianmetalworking.com to watch installments of Automation Talk, a new webcast developed in partnership with Salvagnini America discussing how automation like the S4+P4 changes the nature of the fab shop.
About the Author
subscribe now
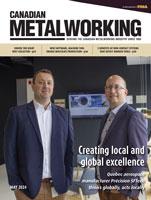
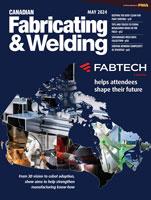
Keep up to date with the latest news, events, and technology for all things metal from our pair of monthly magazines written specifically for Canadian manufacturers!
Start Your Free Subscription- Trending Articles
Aluminum MIG welding wire upgraded with a proprietary and patented surface treatment technology
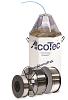
HGG Profiling Equipment BV names Western Canada area sales manager
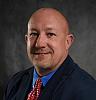
Protected and productive: welding helmet tech
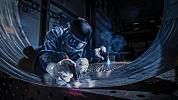
Automotive industry gets back on track
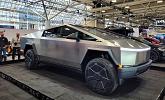
Gas mixer delivers precise mixture adjustments quickly for laser welding
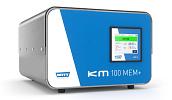
- Industry Events
Automate 2024
- May 6 - 9, 2024
- Chicago, IL
ANCA Open House
- May 7 - 8, 2024
- Wixom, MI
17th annual Joint Open House
- May 8 - 9, 2024
- Oakville and Mississauga, ON Canada
MME Saskatoon
- May 28, 2024
- Saskatoon, SK Canada
CME's Health & Safety Symposium for Manufacturers
- May 29, 2024
- Mississauga, ON Canada