Associate Editor
- FMA
- The Fabricator
- FABTECH
- Canadian Metalworking
Take advantage of pinch turning
Two tools are better than one
- By Lindsay Luminoso
- January 6, 2022
- Article
- Metalworking
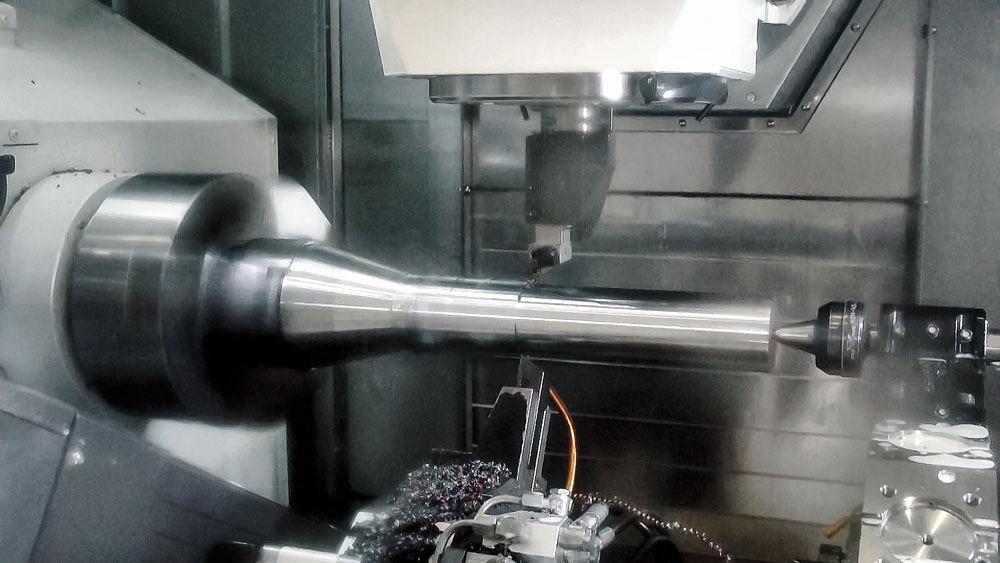
The guiding principle of pinch turning is the ability to put two tools in the cut, so if you can’t do that, then you can’t pinch turn. An obvious requirement for pinch turning is a double-turret machine. Elliott Matsuura Canada
Are two tools better than one? That is a question that many shops interested in pinch turning may ask themselves. But the answer is not a simple yes or no. Pinch turning may sound complicated, but with the right specifications, this operation can be done easily and effectively, cutting cycle time almost in half.
This operation basically allows two tools to access the part simultaneously, one on the top spindle coming down straight and another on the bottom turret coming in at an angle. The tools are staggered, with the second tool coming in at a slightly offset Z-axis position.
For example, with a normal OD pass, the depth of cut (DOC) is split between the two tools during a single pass. The first tool will be positioned for a 0.05-in. DOC, while the second staggered tool—at 0.125-in.offset in Z—will be set for a 0.1-in. DOC. Cycle time is essentially cut in half because the machine is performing two passes at once.
“With pinch turning, the goal is just to go faster and pull off more material in the same amount of time,” said Nick Zentil, director of North American sales, Hexagon Manufacturing Intelligence, North Kingstown, R.I. “Another advantage is its ability to minimize deflection.
When a tool is cutting on one side of the part, there is the risk, especially with long, slender parts, to bend. However, with two forces pushing on both sides, this can reduce the risk of deformation.”
A Balanced Approach
Some manufacturers use the terms pinch turning and balance turning interchangeably. And while these two processes function similarly, there are slight differences between the two. While pinch turning requires two tools to engage the part, balance turning requires the upper spindle and lower turret to engage the part at exactly 180 degrees from each other.
“With balance turning, the tool is able to equalize the passive force of the tool on the direct opposite side of the part during the cutting process,” said Robert Keilmann, senior global product manager for turning, Kennametal, Latrobe, Pa. “Pinch turning, on the other hand, does not require the spindle and the turret to be 180 degrees apart, and therefore does not have the same benefit of passive force equalization. However, it can be applied in applications where high metal removal rates are needed in a short amount of time, making the machine much more cost-effective as it can remove material twice as fast with a shared DOC. Balance turning, with specific machine requirements, is particularly beneficial in thin-walled components or long parts where there is a lack of stability.”
For the most part, balance turning requires that the upper and lower tools cut the same profile at the same DOC simultaneously. Both tools are essentially at the same Z axis, and the toolpath is split between the two tools, allowing for the feed rate to be almost doubled. Pinch turning, alternatively, doubles the DOC, not the feed rate.
Pinch turning should not be confused with a dual-tool operation. Sometimes two tools may be able to cut the part, whether it’s a roughing and drilling operation or something of the like, but pinch turning requires a level of synchronization between tools.
Different Methods
The difference between pinch and balance turning is slight but important, and while many manufacturers use the terminology interchangeably, it’s important to understand the exact operation the machine will be performing before going any further. In general, two different cutting methods can be applied in pinch turning.
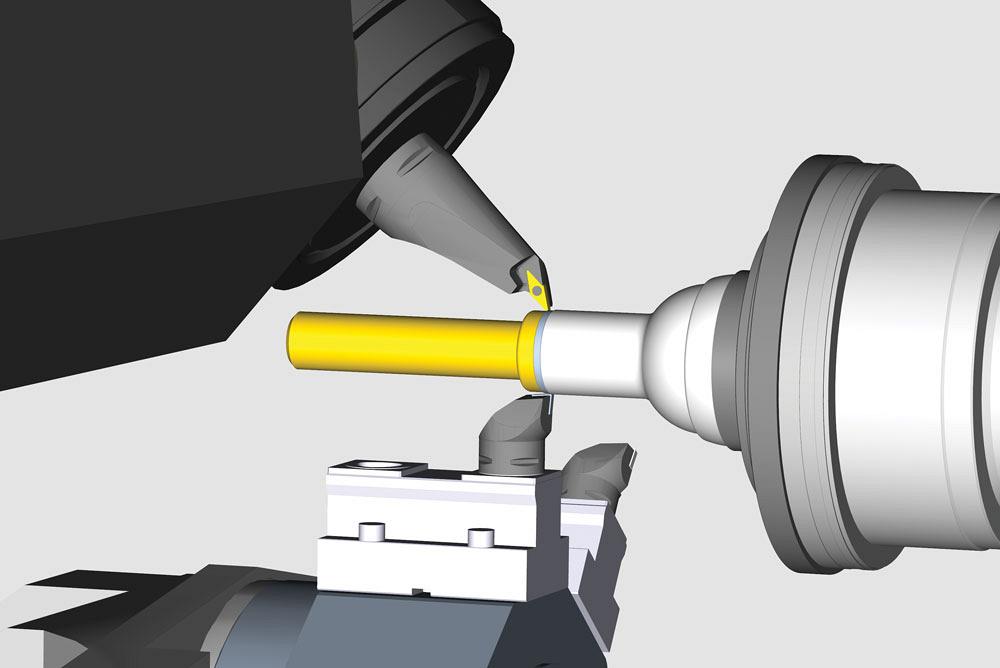
Balance turning requires that the upper and lower tools cut the same profile at the same DOC simultaneously. Both tools are essentially at the same Z axis, and the toolpath is split between the two tools, allowing for the feed rate to be almost doubled. Pinch turning, alternatively, doubles the DOC, not the feed rate. ESPRIT/Hexagon Manufacturing Intelligence
Dual-tool Operations. In a dual-tool operation, during the pinch turning process, both tools are performing the same operation and use the same insert type. For example, on the roughing side, two roughing inserts would be used, slightly offset from one another, and perform the pass staggered, allowing for that larger DOC.
“This is really the easier method of the two,” said Jan Andersson, director of product management, indexable inserts for Americas, YG-1 Canada, Burlington, Ont. “It’s relatively easy to split the larger DOC between the two inserts. With this method, it’s also important to ensure proper synchronization between the upper and lower turret. But one thing you need to be aware of is chip control because you cannot afford to pinch turn with chip control issues.”
The advantage of this process is that you can essentially double the DOC because it removes one pass from the process.
“Cycle time reduction can be fantastic with this approach,” he said. “Pinch turning has much more merit on the dual roughing stage than with something like a roughing-finishing operation. However, it seems that most manufacturers doing pinch turning are not necessarily using two roughing inserts, and instead want one roughing and one finishing.”
Roughing-Finishing Operations. Pinch turning in which the first insert is for roughing and the second for finishing presents its own challenges and is generally used only when surface finish requirements are not particularly high. For the finishing operation, the surface finish generated is directly related to the feed rate and nose radius. So, for the most part, the feed rate should be decreased to generate the necessary surface finish.
“Chip control is defined by chip area (DOC x feed rate) in relation to the elasticity of the material,” said Andersson. “If you have a low feed rate, you have a smaller chip area, which may result in an inability to gain chip control of the roughing insert. You also can’t increase the feed rate on just the rougher because if you do that, you are no longer pinch turning; it will be dissimilar turning. When manufacturers do this type of pinch turning, chip control is always a major struggle. The only way to get around that is to use an insert that can somewhat allow for a lower feed rate on the rougher to match the feed rate on the finisher. And even with that, it can be a struggle.”
With this method of pinch turning, it’s important to find a happy medium where the feed rate satisfied the surface finish requirement. It requires a little more calculation than the standard dual-roughing or dual-finishing method.
Pinch Turn Effectively
Not all machine shops have the capability to pinch turn. And for those that do, it may seem like a daunting operation that is not worth the effort. However, for those that do it, the productivity gains are significant. To perform pinch turning effectively, keep a few things in mind to get the most out of these operations.
Machine Requirements. “One of the most obvious requirements for pinch turning is a double-turret machine,” said Kevin Smith, turning products manager, Elliott Matsuura Canada, Oakville, Ont. “The guiding principle of pinch turning is the ability to put two tools in the cut, so if you can’t do that, then you can’t pinch turn. Pinch turning has long since been performed on a Swiss-style machine. However, it really only applies to the roughing-finishing pinch turning method.”
The machine itself can have an upper and lower turret, an upper spindle and turret, or even a lower turret and live B axis that can be used for turning operations as seen in today’s multitasking machines.
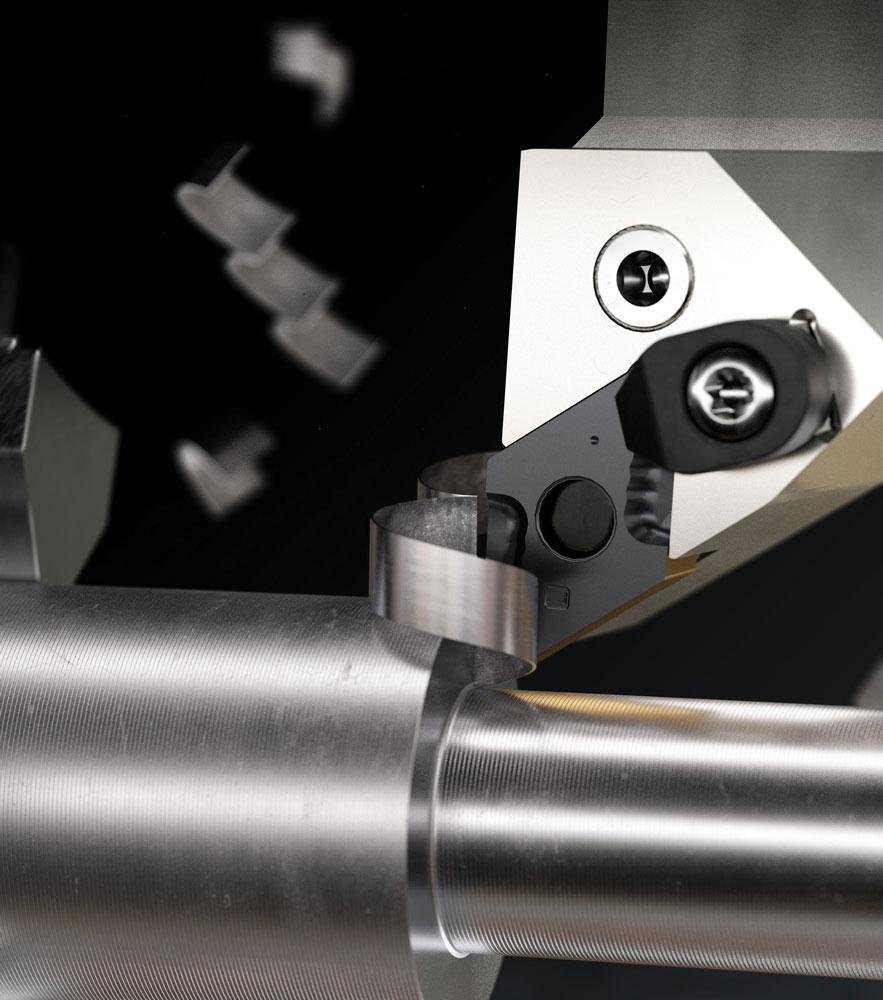
It’s important to select a suitable insert that balances a larger DOC yet retains chip control at a lower feed rate. YG-1 Canada
Because this operation is all about synchronization, it’s important to ensure that the machine’s controls can support it through an M-code that allows the upper and lower turret to follow a single encoder.
“As we see more and more mill-turn machines, with a spindle on top and a turret underneath, penetrating the market, more shops will have the ability to perform pinch turning and simultaneous processes,” said Keilmann.
Keilmann added that having a machine with hard stop capabilities can prevent challenges that come with tool breakage. For example, if a roughing-finishing pinch turn operation is performing heavy roughing, there is potential for the tool to break, and without the hard stop, the finishing tool can also get damaged due to the high load and increased DOC.
Cutting Considerations. One of the first places to start when it comes to cutting considerations is material type. While pinch turning can be used on most materials, some can be more challenging than others.
“There are certain materials that if it’s pushed too hard, it will simply work-harden and then you end up with a catastrophic situation,” said Smith. “Materials like a 15-5 PH [stainless steel] or a 13-8 Mo [stainless steel] will probably not be as suited for pinch turning as a 4140 steel.”
Gummy material can also be a challenge with pinch turning, especially because of chip flow issues. For the most part, with gummy, softer materials like a low-carbon steel, it can be difficult to gain chip control.
“If the chips start wrapping around the part toward the tool coming right behind, it may recut that chip,” said Andersson. “So that’s always a struggle. The chip needs to drop away from the insert sitting right behind. Most components that you would need to pinch turn are long, slender, and commonly low-carbon steels. So that needs to be part of the equation.”
A chipbreaker can be used to manage the chip area and help maintain chip control. However, Andersson noted that with pinch turning, it’s not always about chipbreaking so much as it is about chip steering.
Finding a chip flow that falls away from the secondary edge is crucial to pinch turning success.
Some tools are available that allow for a larger DOC and lower feed rate while still maintaining chip control.
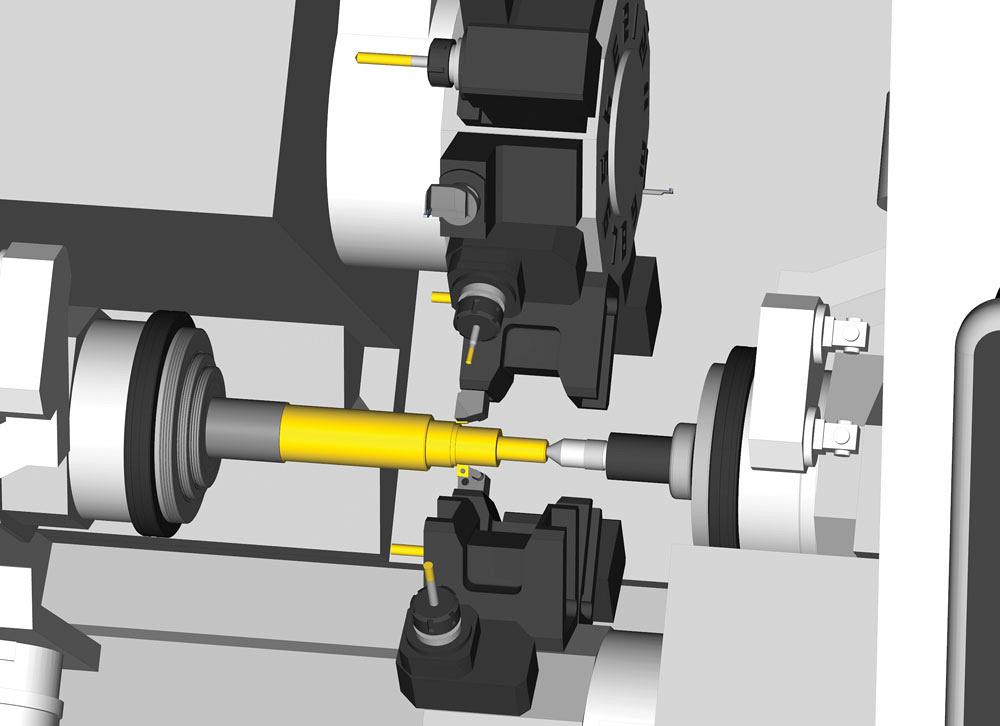
Any shop looking to take on pinch turning should make sure the features and functionalities of the CAM system support it. ESPRIT/Hexagon Manufacturing Intelligence
“As long as you consider the DOC needed in relation to the appropriate insert geometry, style, and size, then you should be fine,” said Keilmann. “For instance, a V-style would not be my first choice for pinch turning, but a C-style insert with a diamond shape of 80 degrees would be much more stable and provide better results.”
When it comes to the roughing-finishing method, Keilmann noted that the right geometry is essential for proper chipbreaking abilities and chip control.
“What you really need to think about with pinch turning is directional force. Basically what you want to have is two opposing forces that balance the operation,” said Andersson. “Increasing the axial forces and decreasing the radial forces will naturally give more stability and make pinch turning easier. With tooling selection, it’s recommended to have a turning insert that is as close to 90 degrees as possible. You don’t want to have a large lead angle, for example, and you want to have greater back clearance on the insert. A smaller lead angle means that you put almost all the forces along the part itself, so you gain natural stability that way too.”
And while pinch turning does tend to be a stable process, it can still be quite demanding on the setup.
It’s important to consider the directional forces and how to maximize the axial force and minimize the radial force during the process.
Programming Parameters. With pinch turning, programming can be a little more complex than for traditional turning. With fewer programmers covering more machines, the added complexity may make it impractical for shops to take on this operation. It also requires quite a bit of process optimization to be successful because of the need to control the forces.
It can be daunting and time-consuming for first-time users, but the gains are significant.
Hexagon’s Zentil noted that one of the hurdles some shops encounter is with programming synchronization between the two turrets as they engage the part.
Some CAM systems will have these sorts of functionalities built in, where the user can select the two turrets and input the pinch turn staggering distance value on the second turret to ensure that the secondary tool follows behind the front tool. However, not all CAM systems may have this functionality. Manual programming can be much more in-depth and require significant calculation as it will not have that same simulation available.
“It’s all about synchronization,” said Smith. “Your CAM system needs to support it and needs to be able to insert a wait code, which acts as a stop sign. If the machine gets to the point where one tool gets ahead of the other, it will read the wait code and the other turret will come and position itself to that same spot so that both tools are leaving at the same time. Most CAM systems have the ability to do that. And certainly any shop looking to take on pinch turning should check the features and functionalities of the CAM system to see if it supports a pinch turning operation.”
Associate Editor Lindsay Luminoso can be reached at lluminoso@canadianmetalworking.com.
Elliott Matsuura, www.elliottmachinery.com
Hexagon Manufacturing Intelligence, www.hexagonmi.com
Kennametal, www.kennametal.com
YG-1, www.yg1.ca
About the Author
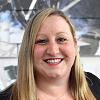
Lindsay Luminoso
1154 Warden Avenue
Toronto, M1R 0A1 Canada
Lindsay Luminoso, associate editor, contributes to both Canadian Metalworking and Canadian Fabricating & Welding. She worked as an associate editor/web editor, at Canadian Metalworking from 2014-2016 and was most recently an associate editor at Design Engineering.
Luminoso has a bachelor of arts from Carleton University, a bachelor of education from Ottawa University, and a graduate certificate in book, magazine, and digital publishing from Centennial College.
subscribe now
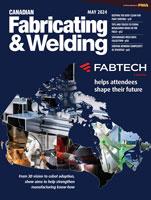
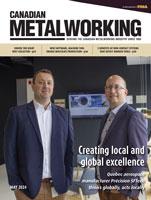
Keep up to date with the latest news, events, and technology for all things metal from our pair of monthly magazines written specifically for Canadian manufacturers!
Start Your Free Subscription- Industry Events
MME Saskatoon
- May 28, 2024
- Saskatoon, SK Canada
CME's Health & Safety Symposium for Manufacturers
- May 29, 2024
- Mississauga, ON Canada
DiPaolo Machine Tools Open House 2024
- June 4 - 5, 2024
- Mississauga, ON Canada
FABTECH Canada
- June 11 - 13, 2024
- Toronto, ON Canada
Zoller Open House & Technology Days 2024
- June 12 - 13, 2024
- Ann Arbor, MI